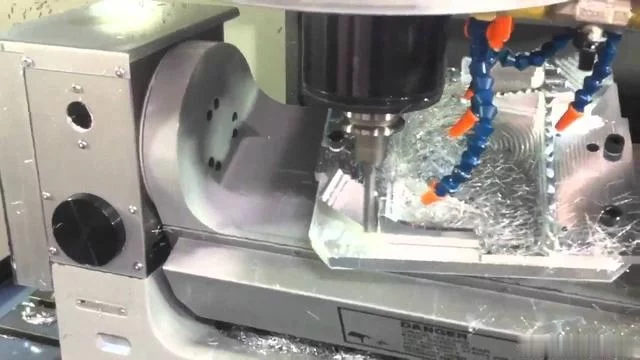
我国数控机床技术与国外的差距究竟是在什么方面?是水平、精度、功能、刚性还是可靠性问题?不妨听听业内人士的看法。
声音一:中国造不了高精度机床的原因是多方面的,但主要原因是缺乏工人和一般的企业培养不了高技能人才。举个简单的例子,培养八级钳工耗资就不是个小数字,而且时间也很长。并且,8级钳工也不能止步不前,也需要时不时去进修一下,另外还要经常给他高难度的工作(小工厂根本培养不起),不然技术会生疏的。总结一下,培养出一个高水平工人,没有5~8年的时间根本办不到,再换一个角度,即使培养出了高水平的工人,如果企业制度不能提供优越的条件,也留不住这样的人才。这就造成了很多工厂不愿意在资金去培养优秀工人。
其次是没有这个精力去设计生产高水平的机床。有时候一台机器造下来要花两三年的时间,以德国为例,以前加工一根卧式铣床的刀具轨需要的工人数为一名工程师,两名技师,3~5名高级工人(大约相当于国内刚拿到8级钳工证的人),而且也非常耗时间,大约要半年(包括精加工和表面处理,以及修配)。
这样下来,除非是大规模企业,小企业根本负担不起这样的开支和时间。以前,国家也不足够重视,所以高精度的机床一直没有太大的进展。不过现在机械工业作为国家工业的基石已经成为最薄弱的一环,各方面已经开始不断重视机械工业的发展。估计不久应该能有较大的进展。
声音二:中国机床差主要是在质量和数控伺服系统,而质量差很多时候是由一个员工的责任感决定的。有很多这样的例子,比如,配合不到就用锤子敲进去,不使用浮动镗来保证孔的型位误差。
另外,数控伺服系统是硬伤。中国主要使用西门子和日本发那科系统,自己的数控系统就差一些,还有主要在伺服电机上的差距。中国的材料也不行,比如,刀具材料无法在6000转以上的环境工作,在新型材料的研究上中国落后了很多,在相同条件下国外的材料和工艺都比我们要好。
一般国产的机床可以使用4~5年,但是要年年校正,用激光校正仪,还有就是精度和容错性比较差,故障处理更是跟不上。还有在航空业使用的机床上有很多设备是专用机床,一般数控机床的精度在0.05mm到0.001mm之间,但是远不能满足高精度零件的加工,只能加工一些中高精度要求的产品,对于象陀螺仪这类零件就需要专用机床。
虚拟机床、快速成型技术、纳米机器这些新技术的出现已经打开了机器制造业新的大门,遗憾的是由于我国电子工业、材料技术的落后,已经落后10~15年了,所以,从某个角度看,我们的机床和国外的机床差距还在加大。